Centre for Applied Research on Technology
At the Centre for Applied Research on Technology, we explore and design technological and tech-driven interventions for a strong, sustainable, liveable and connected Amsterdam Metropolitan Area. We utilise innovative research and a network of partners from the professional field to achieve impact on professional practice. At the same time, we strive to help education stay up-to-date and contribute to training well-equipped technical professionals – the people who can solve the problems of both today and tomorrow.
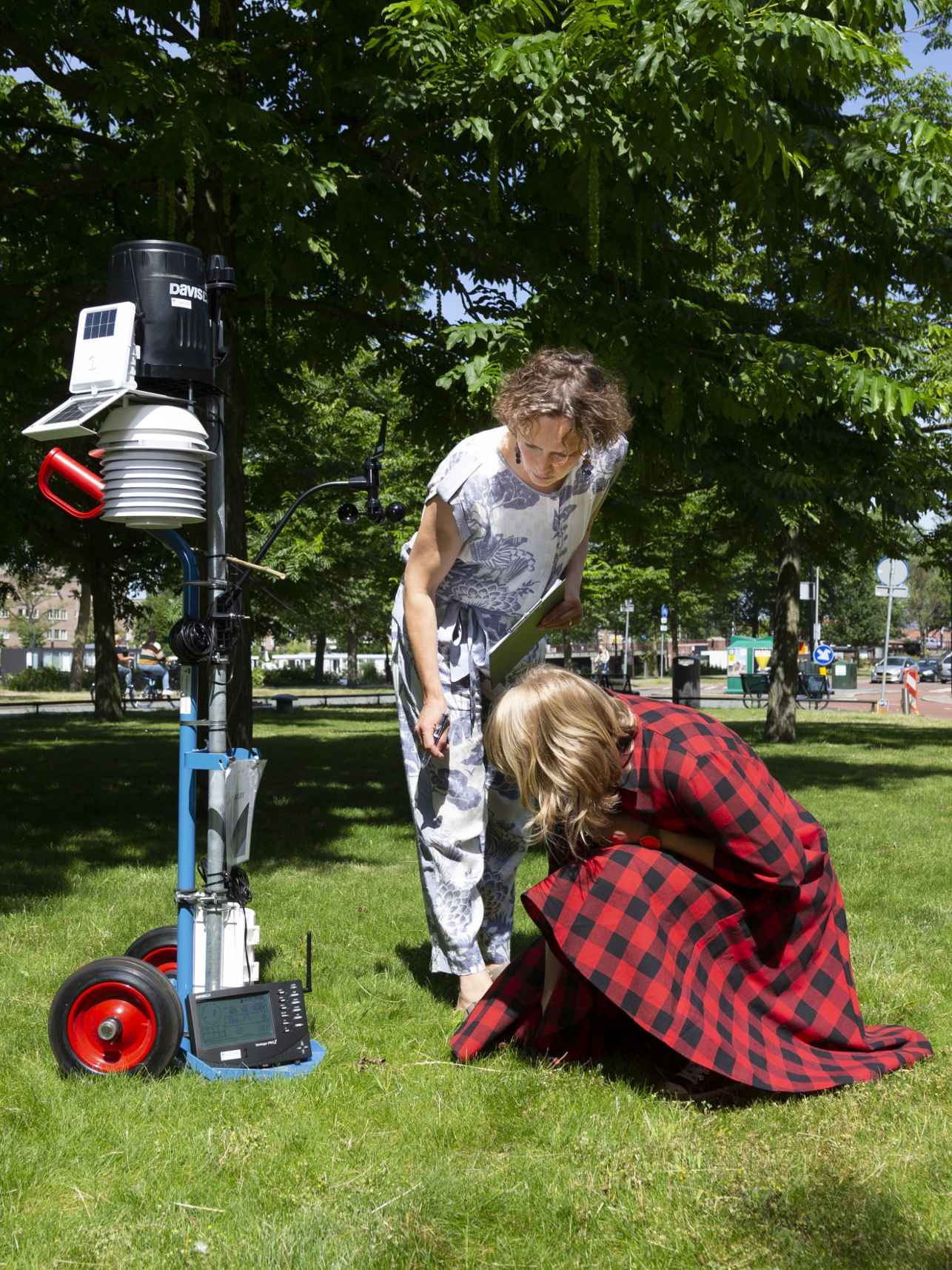
Applied research
Applied research distinguishes itself from academic research through its focus on exploring practical issues from the professional field and intensive cooperation with the professional field during the research. The research is conducted within research groups, which are groups of researchers, including lecturer-researchers, PhD candidates and postdocs, led by a full professor.
Education
Students in HBO Master’s and Bachelor’s programmes frequently take part in the research, for instance in the final phase of the Bachelor, by participating in graduation workshops and collaborating with lecturer-researchers. Methodological thoroughness, connection to academic knowledge and scope for the entire professional field are important principles in the research.
Our research groups
The research groups of the Centre for Applied Research on Technology are:
- Aviation Engineering
- Circular Design and Business (including the research line Digital Production)
- City Logistics
- Climate Resilient City (including the research line Circular Building)
- Digital Forensics
- Energy and Innovation (including the research line Smart Energy Systems)
- Forensic Science
- Forensic Trace Dynamics
- Industrial Digital Twins
- Mainport Logistics
- Spatial Urban Transformation
Impact
Each research project is aimed at achieving impact in the professional field, society and in education. Intensive long-term cooperation with partners – such as professionals who work for municipalities, SMEs and other organisations – also helps to increase the impact in the professional field. In their cooperation with the education sector, the research groups strive to contribute substantially to the renewal of curricula, the content of courses (case studies and contents of classes) and the research skills of students.
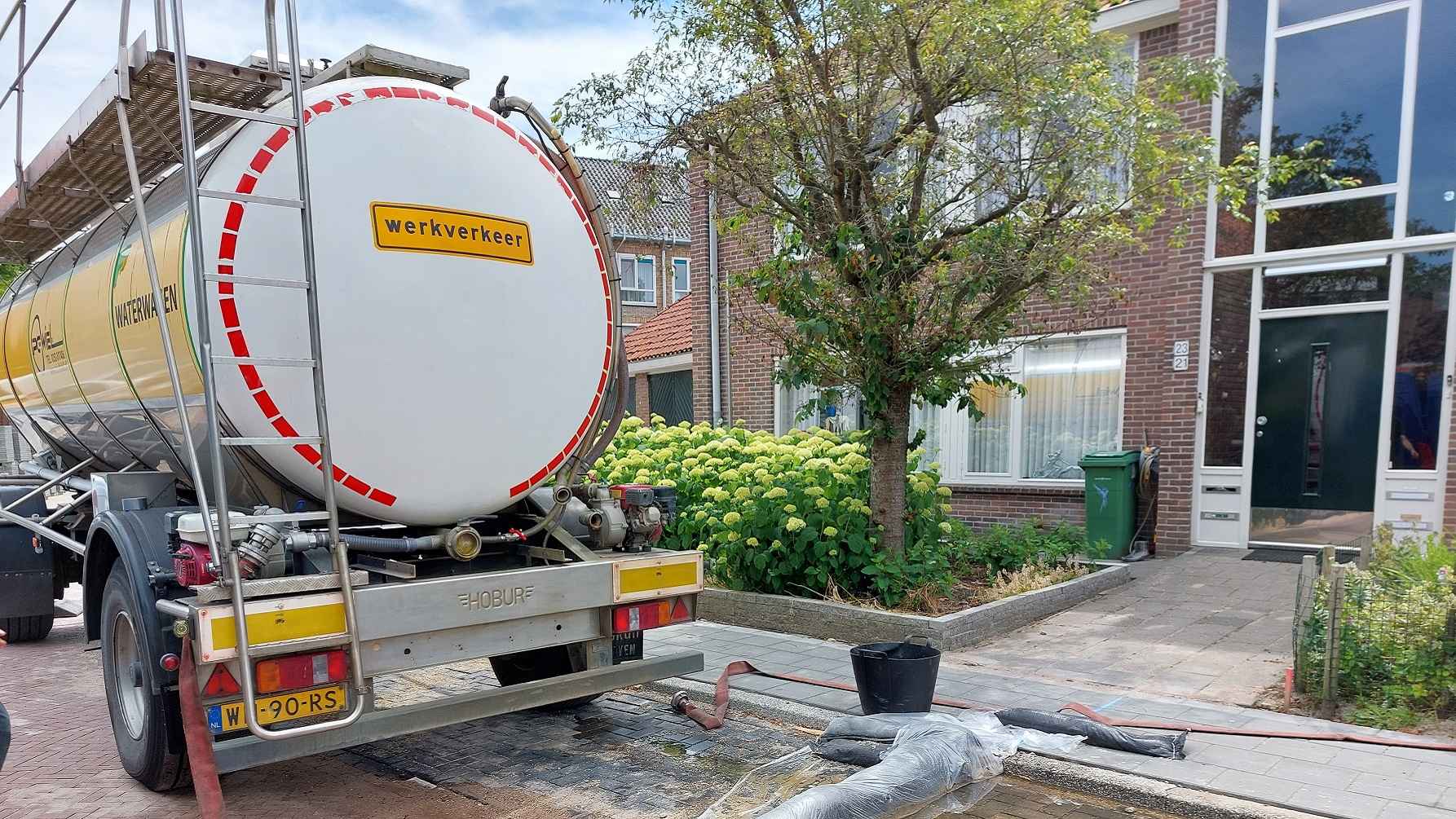
Research characteristics
At the Centre for Applied Research on Technology, we conduct technological research, empirical research and social sciences research. To this end, we apply techniques and methods such as design-based research, field research, experimentation, modelling, data science and prototyping. We also devote attention to human factors and ethical and business aspects to promote the implementation and use of the technological solutions.
Research since 2003
The Faculty of Technology has been conducting research since 2003. It all began with the appointment of a Professor of Logistics. Since that time, various new research groups in the field of technology and technical advancements have been introduced and the impact of the faculty's applied research on people and society has greatly expanded. Today, the research is a cohesive and professional whole.
Centre of Expertise City Net Zero
The Centre for Applied Research on Technology contributes to various Centres of Expertise at AUAS and especially to the Centre of Expertise City Net Zero, for which the Faculty of Technology serves as coordinator.